Uma introdução de Processo de Moldagem por Injeção
A
moldagem por injeção processo inclui principalmente 6 etapas, incluindo fixação do molde, enchimento, retenção de pressão, resfriamento, abertura do molde e desmoldagem. Esses 6 estágios determinam diretamente a qualidade de moldagem do produto, e esses 6 estágios são um processo contínuo completo. Este capítulo se concentra nos quatro estágios de enchimento, pressão de retenção, resfriamento e desmoldagem.
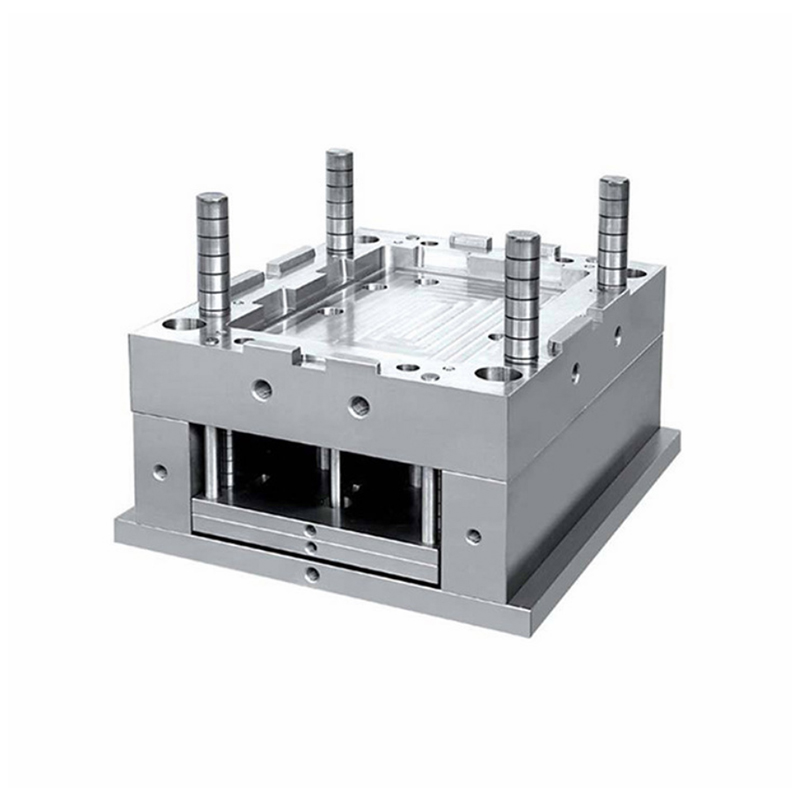
1. Estágio de enchimento
O enchimento é o primeiro passo em todo o ciclo de moldagem por injeção, desde o momento em que o molde é fechado e a injeção é iniciada até que a cavidade do molde seja preenchida até aproximadamente 95%. Em teoria, quanto menor o tempo de enchimento, maior a eficiência de moldagem; mas na produção real, o tempo de moldagem (ou velocidade de injeção) está sujeito a muitas condições.
Enchimento de alta velocidade. Durante o enchimento de alta velocidade, a taxa de cisalhamento é alta e a viscosidade do plástico diminui devido ao efeito do afinamento do cisalhamento, o que reduz a resistência geral ao fluxo; o efeito de aquecimento viscoso local também reduzirá a espessura da camada curada. Portanto, durante a fase de controle de fluxo, o comportamento de enchimento muitas vezes depende do tamanho do volume a ser preenchido. Ou seja, no estágio de controle de fluxo, devido ao enchimento de alta velocidade, o efeito de afinamento de cisalhamento da massa fundida é geralmente grande e o efeito de resfriamento da parede fina não é óbvio, de modo que o efeito da velocidade prevalece.
Encha em baixa velocidade. Controle de condução de calor Ao encher em baixa velocidade, a taxa de cisalhamento é menor, a viscosidade local é maior e a resistência ao fluxo é maior. Devido à baixa taxa de reabastecimento e fluxo lento do termoplástico, o efeito de condução de calor é mais óbvio e o calor é rapidamente retirado pela parede fria do molde. Combinado com uma quantidade menor de aquecimento viscoso, a camada solidificada é mais espessa, o que aumenta ainda mais a resistência ao fluxo na parede mais fina.
Devido ao fluxo de fonte, as cadeias de polímeros plásticos na frente da onda de fluxo estão alinhadas quase paralelamente à frente da onda de fluxo. Portanto, quando os dois filamentos de plástico fundido se encontram, as cadeias de polímero na superfície de contato são paralelas uma à outra; além disso, as propriedades das duas vertentes do fundido são diferentes (o tempo de residência na cavidade do molde é diferente e a temperatura e a pressão também são diferentes), resultando na área de fusão do fundido. Microscopicamente, a resistência estrutural é pobre. Quando as peças são colocadas em um ângulo apropriado sob a luz e observadas a olho nu, pode-se verificar que existem linhas de ligação óbvias, que é o mecanismo de formação da linha de solda. A linha de solda não afeta apenas a aparência da peça plástica, mas também sua microestrutura fica frouxa, o que facilita a concentração de tensões, de modo que a resistência da peça é reduzida e ocorre a fratura.
De um modo geral, a resistência da linha de solda que produz a solda na região de alta temperatura é melhor. Porque em alta temperatura, a mobilidade das cadeias poliméricas é relativamente boa, e elas podem penetrar e se entrelaçar. Além disso, a temperatura dos dois fundidos na área de alta temperatura é relativamente próxima e as propriedades térmicas dos fundidos são quase as mesmas, o que aumenta a resistência da área de soldagem. Na área de baixa temperatura, a força de soldagem é pobre.
2. Palco de retenção
A função do estágio de empacotamento é aplicar pressão continuamente para compactar o fundido e aumentar a densidade do plástico (densificação) para compensar o comportamento de contração do plástico. Durante o processo de retenção de pressão, a contrapressão é alta porque a cavidade do molde já está preenchida com plástico. No processo de retenção de pressão e compactação, o parafuso da máquina de moldagem por injeção só pode avançar lentamente e ligeiramente, e a velocidade de fluxo do plástico também é relativamente lenta. O fluxo neste momento é chamado de fluxo de pressão de retenção. No estágio de retenção de pressão, o plástico é resfriado e solidificado mais rapidamente pela parede do molde, e a viscosidade do fundido aumenta rapidamente, de modo que a resistência na cavidade do molde é muito grande. No estágio posterior da pressão de retenção, a densidade do material continua a aumentar e as peças plásticas são gradualmente formadas. O estágio de retenção de pressão continua até que o portão esteja curado e selado. Neste momento, a pressão da cavidade no estágio de retenção de pressão atinge o valor mais alto.
Durante a fase de empacotamento, o plástico apresenta propriedades parcialmente compressíveis devido à pressão relativamente alta. Em áreas de maior pressão, o plástico é cada vez mais denso; em áreas de menor pressão, o plástico é mais solto e de menor densidade, resultando em uma mudança na distribuição de densidade com a localização e o tempo. Durante o processo de retenção de pressão, a vazão do plástico é extremamente baixa e a vazão não desempenha mais um papel de liderança; a pressão é o principal fator que afeta o processo de retenção de pressão. Durante o processo de retenção de pressão, o plástico encheu a cavidade do molde e a massa fundida gradualmente solidificada é usada como meio para transmitir a pressão. A pressão na cavidade do molde é transmitida para a superfície da parede do molde através do plástico, e há uma tendência de abertura do molde, sendo necessária uma força de fixação adequada para a fixação do molde. Em circunstâncias normais, a força de expansão do molde abrirá ligeiramente o molde, o que é útil para a exaustão do molde; mas se a força de expansão do molde for muito grande, é fácil causar rebarbas, transbordamento do produto moldado e até mesmo abrir o molde. Portanto, ao selecionar uma máquina de moldagem por injeção, uma máquina de moldagem por injeção com força de fixação suficiente deve ser selecionada para evitar a expansão do molde e manter a pressão de forma eficaz.
No novo ambiente de moldagem por injeção, precisamos considerar alguns novos processos de moldagem por injeção, como moldagem assistida por gás, moldagem assistida por água, moldagem por injeção de espuma, etc.
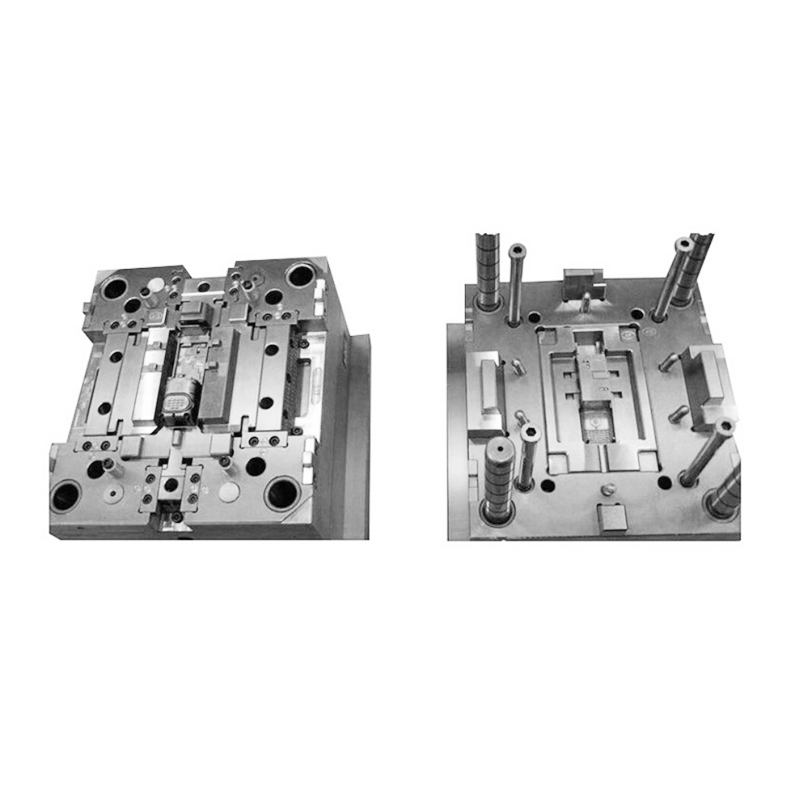
3. Estágio de resfriamento
Em moldes de moldagem por injeção, o projeto do sistema de refrigeração é muito importante. Isso ocorre porque o produto plástico moldado só pode ser resfriado e solidificado até uma certa rigidez, e o produto plástico pode ser impedido de ser deformado por força externa após a desmoldagem. Como o tempo de resfriamento é responsável por cerca de 70% a 80% de todo o ciclo de moldagem, um sistema de resfriamento bem projetado pode encurtar bastante o tempo de moldagem, melhorar a produtividade da injeção e reduzir custos. O sistema de refrigeração mal projetado prolongará o tempo de moldagem e aumentará o custo; o resfriamento desigual causará ainda mais o empenamento dos produtos plásticos.
De acordo com o experimento, o calor do fundido que entra no molde é geralmente dissipado em duas partes, uma parte é 5% transferida para a atmosfera por radiação e convecção, e os 95% restantes são conduzidos do fundido para o molde. Devido ao tubo de água de resfriamento no molde, o calor é transferido do plástico na cavidade do molde para o tubo de água de resfriamento através da estrutura do molde por condução de calor e, em seguida, retirado pelo líquido de resfriamento por convecção térmica. Uma pequena quantidade de calor que não é retirada pela água de resfriamento continua a ser conduzida no molde e, em seguida, se dissipa no ar após entrar em contato com o mundo exterior.
O ciclo de moldagem da moldagem por injeção consiste no tempo de fixação do molde, tempo de enchimento, tempo de retenção de pressão, tempo de resfriamento e tempo de desmoldagem. Dentre eles, o tempo de resfriamento representa a maior proporção, que gira em torno de 70% a 80%. Portanto, o tempo de resfriamento afetará diretamente a duração do ciclo de moldagem e a produção de produtos plásticos. Na fase de desmoldagem, a temperatura do produto plástico deve ser resfriada a uma temperatura inferior à temperatura de deformação térmica do produto plástico para evitar que o produto plástico se solte devido a tensão residual ou empenamento e deformação causada pela força externa da desmoldagem.
Os fatores que afetam a taxa de resfriamento do produto são:
1) Design de produtos plásticos. Principalmente a espessura da parede de produtos plásticos. Quanto mais espesso o produto, maior o tempo de resfriamento. De um modo geral, o tempo de resfriamento é aproximadamente proporcional ao quadrado da espessura do produto plástico, ou à potência 1.6 do diâmetro máximo do canal. Ou seja, a espessura do produto plástico é dobrada e o tempo de resfriamento é aumentado em 4 vezes.
2) O material do molde e seu método de resfriamento. O material do molde, incluindo o núcleo do molde, o material da cavidade e o material da base do molde tem uma grande influência na taxa de resfriamento. Quanto maior a condutividade térmica do material do molde, melhor o efeito de transferência de calor do plástico por unidade de tempo e menor o tempo de resfriamento.
3) A configuração dos tubos de água de refrigeração. Quanto mais próximo o tubo de água de resfriamento estiver da cavidade do molde, maior o diâmetro do tubo e quanto maior o número, melhor o efeito de resfriamento e menor o tempo de resfriamento.
4) Fluxo de refrigerante. Quanto maior a taxa de fluxo da água de resfriamento (geralmente melhor para obter fluxo turbulento), melhor o efeito da água de resfriamento para remover o calor por convecção térmica.
5) A natureza do refrigerante. A viscosidade e a condutividade térmica do refrigerante também afetarão a condutividade térmica do molde. Quanto menor a viscosidade do refrigerante, maior a condutividade térmica e quanto menor a temperatura, melhor o efeito de resfriamento.
6) Escolha de plástico. Plástico refere-se a uma medida de quão rapidamente o plástico conduz o calor de um lugar quente para um lugar frio. Quanto maior a condutividade térmica do plástico, melhor o efeito de condução térmica, ou quanto menor o calor específico do plástico, mais fácil é a mudança de temperatura, então o calor é fácil de dissipar, o efeito de condução térmica é melhor e o tempo de resfriamento necessário é menor.
7) Configuração de parâmetros de processamento. Quanto maior a temperatura do material, maior a temperatura do molde, menor a temperatura de ejeção e maior o tempo de resfriamento necessário.
Regras de projeto para sistemas de refrigeração:
1) O canal de resfriamento é projetado para garantir que o efeito de resfriamento seja uniforme e rápido.
2) O objetivo de projetar o sistema de resfriamento é manter o resfriamento adequado e eficiente do molde. Os furos de resfriamento devem ser de tamanho padrão para facilitar a usinagem e a montagem.
3) Ao projetar um sistema de resfriamento, o projetista do molde deve determinar os seguintes parâmetros de projeto de acordo com a espessura da parede e o volume da peça plástica - a localização e o tamanho do orifício de resfriamento, o comprimento do orifício, o tipo de orifício, a configuração e conexão do furo, e a vazão e vazão do líquido de resfriamento. propriedades de transferência de calor.
4. Estágio de desmoldagem
A desmoldagem é o último elo de um ciclo de moldagem por injeção. Embora o produto tenha sido endurecido a frio, a desmoldagem ainda tem um impacto muito importante na qualidade do produto. O método de desmoldagem inadequado pode causar tensão desigual no produto durante a desmoldagem e causar defeitos como deformação do produto durante a ejeção. Existem duas formas principais de desmoldagem: desmoldagem do ejetor e desmoldagem da placa de decapagem. Ao projetar um molde, um método de desmoldagem apropriado deve ser selecionado de acordo com as características estruturais do produto para garantir a qualidade do produto.
Para o molde com ejetor ejetor, os pinos ejetores devem ser ajustados o mais uniforme possível, e a localização deve ser selecionada no local de maior resistência à ejeção e maior resistência e rigidez das peças plásticas, de modo a evitar deformações e danos das peças plásticas. A placa stripper é geralmente utilizada para a desmoldagem de recipientes de paredes finas com cavidades profundas e produtos transparentes que não permitem vestígios de varetas.
Ningbo Fuerd foi fundada em 1987, é líder de serviço completo Ferramentas de fundição, fundição de alumínio, fundição de zinco, Fundição por gravidade fabricante. Somos um provedor de soluções que oferece uma ampla gama de recursos e serviços que incluem suporte de engenharia, concepção, moldescomplexo usinagem CNC, impregnação, tamboreamento, cromo, pintura a pó, polimento, montagem e outros serviços de acabamento. Trabalharemos com você como parceiros, não apenas fornecedores.